SSSSS
Five Japanese terms and their alliterative English equivalents helped bring order to a hospital command center.
There's some debate about whether the origin of lean production lies in a 16th-century Venetian shipyard or a Toyota plant in the 1970s. But either way, application of the five S's involves standardization and continuous monitoring in order to improve efficiency and safety and eliminate waste.
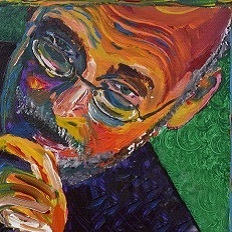
The S's refer to five Japanese terms that have been translated into alliterative equivalents in English.
Seiri/Sort
Seiri is the process of separating the supplies and equipment that are needed to do a day's work from the items that are unneeded, expired, or damaged, then discarding the latter group. In essence, it is the art of decluttering.
Seiton/Set in Order
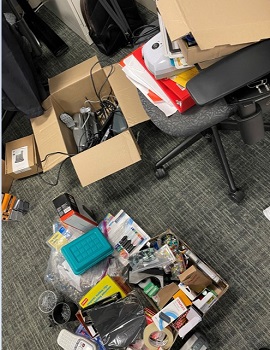
Seiton involves finding a home for every item. The goal is to neatly arrange all your supplies and equipment in the best place for efficiency and ease of use. The items used most frequently should be closest to hand, while those that are very rarely used should have a home that is more distant from the center of the action. Those you never use should be recycled, restored, or refused (i.e., put in the trash).
Seiso/Shine
Seiso is the act of cleaning a space, mapping out where items should be placed and in what quantity, and providing visual cues for restocking to maintain function. If you don't know where things are, they get reordered, or you spend hours looking for them (like one of the authors did this morning for his wallet). Everything in its place, and a place for everything.
Seiketsu/Standardize
Seiketsu is a way to make sure that the first three S's happen on a regular basis. Setting a workplace standard with visual cues and training to maintain the perfect condition is key to success. Your efforts will be wasted without diligence to seiketsu.
Shitsuke/Sustain
Shitsuke is the process of upholding the first four S's, and in many ways the hardest step. An auditing system should be built to maintain supplies at desired quantities and replace items when they're used, preventing gradual decline back to chaos, as well as enabling continuous improvement.
In our Rochester Hospital Operations Command Center, we recently went through these five steps, with great results, filling an entire dumpster with a decade's worth of tired, expired, and undesired items. The level of enthusiasm and fun hospital staff found in this activity was surprising. The highlight was disposing of a massive binder and clear plastic folders that had been filling a cabinet with downtime instructions for an information system that had been deactivated many years ago. If anyone needs 150 plastic folders, let us know!